Milling: Difference between revisions
m (→Gap Setting) Tags: Mobile edit Mobile web edit |
m (ref fix) |
||
(439 intermediate revisions by 2 users not shown) | |||
Line 1: | Line 1: | ||
(In | [[Category:Wort production]] [[Category:Equipment and maintenance]] | ||
[[File:Grain-milled.png|thumb|Milled grain. Photo by Bryan Rabe.]] | |||
[[Grain]] consists mainly of [[starch]] granules (endosperm) inside a husk. Before the [[mashing|mash]], grain must be mechanically crushed using a mill. The crushing process breaks open the husks, exposing the starch, and also cracks the starch into smaller bits, increasing the surface area exposed to water and [[enzymes]] during mashing.<ref name=mostra>Mosher M, Trantham K. [[library|''Brewing Science: A Multidisciplinary Approach.'']] 2nd ed. Springer; 2021.</ref> The crushed grain is referred to as ''grist''. In general, the crush quality affects the [[mashing|mashing process]], including [[starch|saccharification]] time, [[lautering]], [[efficiency]], [[fermentation]], as well as the color, taste, and overall character of the beer.<ref name="Kunze">Kunze W. Wort production. In: Hendel O, ed. [[Library|''Technology Brewing & Malting.'']] 6th ed. VLB Berlin; 2019:203–218.</ref><ref name="Mousia">Mousia Z, Balkin RC, Pandiella SS, Webb C. [https://www.sciencedirect.com/science/article/pii/S0032959203004400 The effect of milling parameters on starch hydrolysis of milled malt in the brewing process.] ''Process Biochem.'' 2004;39(12):2213–2219.</ref> | |||
[[ | Milling Process Overview: | ||
# '''Weigh''' the grain on a [[scale]] per the recipe specifications. | |||
# '''Condition''' the grain (optional) | |||
# '''Crush''' the grain by adding it to the hopper and spinning the drive roller. The grist must be collected in a bucket or milled directly into the mash vessel. | |||
# '''Verify''' the crush by visual inspection. It's generally a good idea to inspect the first handful of grain before continuing with the rest. | |||
==Grain mills== | |||
Why own a mill? | |||
* '''Freshness''' - Milling immediately before brewing results in the freshest malt possible (helping to avoid [[oxidation]]). | |||
* '''Control''' - Adjusting the gap allows you to tailor the crush to your own system and maximize [[efficiency]]. | |||
* '''Consistency''' - The crush size may be inconsistent with pre-milled grain. | |||
* '''Grain conditioning''' - Milling on site gives you the option to condition your grain (see below). | |||
* '''Cost savings''' - A personal grain mill eventually pays for itself because A) you avoid a milling fee and B) you can buy grain in bulk. | |||
== | === Features === | ||
[[File:Knurled-rollers.jpg|thumb|right|Knurled rollers on a 3-roller mill (bottom view)]] | |||
*'''3-roller vs 2-roller''' - In a 3-roller mill, the grain is pre-crushed in the gap between the top two rollers, and then the grain flows into the gap between the drive roller and bottom roller, crushing it further. The top gap is fixed at around 0.060–0.070" which easily pulls in both wheat and barley, providing superior feed, and softening the starch without tearing up the husk.<ref name="monster">[https://www.monsterbrewinghardware.com/store/pc/FAQs-d2.htm FAQs.] Monster Brewing Hardware. Accessed May 2020.</ref> The lowered husk damage aids in lautering among other things (see below). The double crush also more fully separates the husk from the starch. The downsides to 3-roller mills are that more power (torque) is typically required to drive them and they are generally more expensive. 2-roller mills are more budget friendly. | |||
*'''Bearings vs bushings''' - Sealed ball bearings generally require no maintenance and can have a significantly longer lifespan than bushings, particularly if you drive the mill with a pulley.<ref>[https://www.homebrewtalk.com/threads/grain-mill-recomendations.662727/post-8529641 Grain mill recomendations.] Homebrew Talk website. 2019. Accessed 2020.</ref><ref>[https://www.homebrewtalk.com/threads/quality-corona-hand-crank-mill.645349/post-8224674 Quality corona/hand-crank mill?] Homebrew Talk website. 2018. Accessed 2020.</ref><ref>[https://www.homebrewtalk.com/threads/tell-me-about-grain-mills.666252/post-8598698 Tell me about grain mills.] Homebrew Talk website. 2019. Accessed 2020.</ref><ref>[https://www.homebrewtalk.com/threads/grain-mill-recomendation.672926/post-8734778 Grain mill recomendation.] Homebrew Talk website. 2019. Accessed 2020.</ref> On the other hand, bushings have more friction and may wear over time, such that they will need to be replaced at some point.<ref>Layosa C. [https://blog.misumiusa.com/introduction-to-working-with-linear-bushings-bushings-vs-bearings/ Introduction to working with linear bushings: bushings vs. bearings.] Misumi website. 2016. Accessed 2020.</ref><ref>[https://youtu.be/fJVGlvZQvGk Ball Bearings vs Bushings.] ServoCity on YouTube. 2017. Accessed 2020.</ref> Therefore we recommend a mill with sealed ball bearings. However, bushings are still an acceptable option when using a direct drive system such as a drill. Bushings may benefit from periodic cleaning and lubrication with a drop of food-grade mineral oil; check with the manufacturer.<ref name="LOB-1069">[http://www.themodernbrewhouse.com/forum/viewtopic.php?f=18&t=1069 Choosing a malt mill.] The Modern Brewhouse website. 2018–2020. Accessed 2020.</ref><ref>[https://www.homebrewtalk.com/threads/monster-mill-problems.102809/post-1141303 Monster mill problems.] Homebrew Talk website. 2009. Accessed 2020.</ref> | |||
*'''Roller material''' - For most brewers, hardened steel is the best option for roller material due to its durability.<ref>[https://www.reliance-foundry.com/blog/carbon-steel-versus-stainless-steel Carbon steel vs stainless steel.] Reliance Foundry. Accessed June 2020.</ref> However, stainless steel has better protection against corrosion (although it is also more expensive). If you live in a damp or coastal region, stainless might be a good option.<ref>[https://www.monsterbrewinghardware.com/store/pc/3-Roller-Homebrew-Grain-Mill-p86.htm 3 roller homebrew grain mill.] Monster Brewing Hardware. Accessed June 2020.</ref> | |||
* | *'''Roller diameter''' - Larger diameter helps the grain feed through the rollers.<ref name="Kunze"/><ref name=mashing>Evans E. [[Library|''Mashing.'']] American Society of Brewing Chemists and Master Brewers Association of the Americas; 2021.</ref> | ||
*'''Knurled vs fluted rollers''' - Roller morphology has an important effect on the crush by reducing damage to the husk. Modern ''commercial'' mills always have fluted rollers.<ref name=Mousia/><ref name=Kunze/><ref name=hob11>Miedl-Appelbee M. Brewhouse technology. In: Stewart GG, Russell I, Anstruther A, eds. [[Library|''Handbook of Brewing.'']] 3rd ed. CRC Press; 2017.</ref> On the other hand, most home brew mills have rollers with a diamond knurling pattern, which is necessary to improve the grain feed through small diameter rollers. A few home brew mills with relatively larger rollers (e.g. MattMill and Ss Brewtech) have a fluted morphology. However, the fluting pattern on these is completely different than commercial mills,<ref name=Kunze/> so it is unclear whether the fluting provides any benefit over knurling for home milling. | |||
*'''Drive shaft''' - A 1/2" integrated drive shaft is the most durable. If you have a drill that you plan to use for milling, verify that it can fit on the drive shaft for the mill you want to purchase. (See [[Milling#Driving the mill|Driving the mill]] below) | |||
*'''Hopper size''' - Hopper size is a matter of convenience and budget. It is most convenient to add the grain to the hopper all at once, however it doesn't hurt anything if you need to pause partway through milling in order to fill the hopper with more grain. Portability, weight, and storage space should be also be taken into account. Some mills have optional hopper extensions to purchase, or you can make a hopper extension yourself. | |||
*'''Throughput rate''' - Differences in roller length and how fast the rollers feed grain is generally negligible for home brewers and not something that needs to be considered. Throughput depends largely on drive speed (RPM) and not the particular mill characteristics. | |||
*'''Roller speed differential''' - Modern large-scale commercial mills have the rollers spinning at different speeds.<ref name=Kunze/> This increases the effectiveness of the crush by shearing off the husk from the endosperm, which serves to increase yield while reducing husk damage.<ref name=Mousia/> The only home brew mill with speed differential is from Ss Brewtech. | |||
* | |||
* | |||
=== | === Best mills available === | ||
* | {| class="wikitable" | ||
!colspan="5"|2-Roller Mills | |||
|- | |||
!Mill | |||
!Rollers | |||
!Bearing type | |||
!Accessories | |||
!Where to purchase | |||
|- style="vertical-align:top;" | |||
|[[File:Star-6-16.png|right|alt=star]]Cereal Killer, <br/>Kegco 2, <br/>Hullwrecker, <br/>Malt Muncher 2 <br/>(All the same) | |||
|Knurled 1.25" x 5" hardened steel | |||
|Sealed ball bearings | |||
|Includes 7lb hopper and hand crank | |||
| | |||
* {{Amazon|B014M8WQIY}} (includes base) | |||
* [https://www.homebrewing.org/Cereal-Killer-Grain-Mill_p_2310.html AIH] (includes base) | |||
* [https://www.beveragefactory.com/homebrew/pre-fermentation-equipment/kegco-KM7GM-2R-grain-mill.html Beverage Factory] (includes base) | |||
* [https://www.austinhomebrew.com/Cereal-Killer-Grain-Mill_p_4432.html Austin Homebrew Supply] (includes base) | |||
* [https://www.northernbrewer.com/collections/grain-mills/products/hullwrecker-2-roller-grain-mill-base Northern Brewer] (includes base) | |||
* {{MB|malt-muncher-2-roller-grain-mill}} | |||
* {{MB|motorized-maltmuncher-pro-1}} (Motorized) | |||
* {{Amazon|B074D9TP8B}} | |||
|- style="vertical-align:top;" | |||
|Monster Mill 2 | |||
|Knurled 1.5" x 6" hardened steel or stainless steel optional | |||
|Bronze bushings | |||
|11lb hopper, hopper extension, hand crank, and base are all optional. | |||
| | |||
*[https://www.monsterbrewinghardware.com/store/pc/2-Roller-Homebrew-Grain-Mill-p69.htm Monster Brewing] | |||
|- style="vertical-align:top;" | |||
|MattMill Kompakt | |||
|Fluted 2.75" x 2" hardened steel | |||
|Roller bearings<ref>[http://www.mattmill.de/wp-content/uploads/2018/12/MattMill-Docu-MMKP-MMKO-2018-EN.pdf "MattMill Kompakt / Kompakt Komfort documentation."] MattMill. 2018. Accessed 2020.</ref> | |||
|Hand crank and base are optional and hopper is generally DIY. | |||
| | |||
*[https://www.austinhomebrew.com/MattMill-Kompakt-Grain-Mill_p_7192.html Austin Homebrew Supply] | |||
|- | |||
!colspan="5"|3-Roller Mills | |||
|- | |||
!Mill | |||
!Rollers | |||
!Bearing type | |||
!Accessories | |||
!Where to purchase | |||
|- style="vertical-align:top;" | |||
|[[File:Star-6-16.png|right|alt=star]]Kegco 3, <br/>Malt Muncher 3 <br/>(same) | |||
|Knurled 1.5" x 6" hardened steel | |||
|Sealed ball bearings | |||
|Includes 12lb hopper and hand crank. Base is optional. | |||
| | |||
*[https://www.beveragefactory.com/homebrew/pre-fermentation-equipment/kegco-km11gm-3r-grain-mill.html Beverage Factory] (includes base) | |||
*{{Amazon|B014M8WS14}} (includes base) | |||
*{{MB|malt-muncher-3-roller-grain-mill}} | |||
*{{Amazon|B074DBJR8X}} | |||
*[https://www.brewhardware.com/product_p/grainmill3roller.htm Brew Hardware] | |||
*[https://www.williamsbrewing.com/Home-Brewing-Equipment/Wort-Making-Equipment/Grain-Mills/Maltmuncher-Three-Roller-Mill William's Brewing] | |||
|- style="vertical-align:top;" | |||
|Monster Mill 3 | |||
|Knurled 1.5" x 6" hardened steel or stainless steel optional | |||
|Bronze bushings | |||
|11lb hopper, hopper extension, base, and hand crank are all optional. | |||
| | |||
*{{Amazon|B017MR35MS}} | |||
*[https://www.monsterbrewinghardware.com/store/pc/3-Roller-Homebrew-Grain-Mill-10p86.htm Monster Brewing] | |||
|- | |||
!colspan="5"|Premium Motorized Mills | |||
|- | |||
!Mill | |||
!Rollers | |||
!Bearing type | |||
!Accessories | |||
!Where to purchase | |||
|- style="vertical-align:top;" | |||
|Ss Brewtech | |||
|Fluted 4" diameter stainless steel, with speed differential | |||
|Sealed ball bearings | |||
|Includes motor and 25lb hopper. Base/cart is optional. | |||
| | |||
* {{MB|ss-brewtech-grain-mill}} | |||
|- style="vertical-align:top;" | |||
|MoreBeer UltiMill | |||
|Knurled 2" diameter hardened steel | |||
|Unknown | |||
|Includes 60lb hopper with lid, motor, and stand. | |||
| | |||
*{{MB|ultimill-ultimate-grain-mill-3}} | |||
|} | |||
[[File:Star-6-16.png|alt=star]] = Editor's Pick | |||
Crankandstein has a few barebones mills that are suited to the DIY-inclined brewer. You can get a basic mill and mount it in any mill housing design of your choice. They offer a [https://www.crankandstein.net/index.php?main_page=product_info&cPath=7&products_id=11 2-roller] mill, [https://www.crankandstein.net/index.php?main_page=product_info&cPath=7&products_id=13 3-roller] mill, and a [https://www.crankandstein.net/index.php?main_page=product_info&cPath=6&products_id=9 2-roller mill that can also crush corn]. All of these have knurled hardened steel rollers and bronze bushings. | |||
=== Mills to avoid === | |||
*'''The Barley Crusher''' - It has soft rollers and soft/cheap bronze bushings, which lead to relatively frequent problems and a short product lifespan.<ref>[https://www.homebrewtalk.com/threads/grain-mill-stopped-working.654248/ Grain mill stopped working.] Homebrew Talk website. 2018. Accessed 2020.</ref> Their customer service is also very poor.<ref>Barley Crusher - customer service???? Homebrew Talk website. 2012–2018. Accessed 2020. (This webpage has since been deleted. That's one more reason not to trust homebrewtalk.com)</ref> | |||
*'''Suspicious budget mills''' such as the [https://www.vevor.com/products/electric-grain-mill-barley-grinder-malt-crusher-hold-up-to-11lbs-crushing-dy-368 motorized] and [https://www.vevor.com/products/grain-mill-barley-grinder-malt-crusher-3-roller-wheat-home-brew-food-industry 3-roller] mills at Vevor - These cheap mills have a number of {{amazon|B07D1Y51WT|bad reviews}} and generally don't have a strong track record, so we don't recommend these products at this time.<ref>[https://www.homebrewtalk.com/threads/anyone-try-those-cheap-ebay-motorized-grain-mills.688262/ Anyone try those cheap eBay motorized grain mills?] Homebrew Talk website. 2020–2021. Accessed Jan 4 2021.</ref> | |||
*'''Non-roller mills''' such as food processors, rolling pins, or Corona/Victoria style disc mills ({{Amazon|B00JZZKLHI|example}})<ref>[https://www.homebrewtalk.com/threads/my-ugly-junk-corona-mill-station.90849/ My ugly junk- Corona mill station.] Homebrew Talk website. 2008–2020. Accessed 2020.</ref> - These tools are not designed to create a proper crush, they're not easily adjustable, they tend to create a mess and/or require significant modification just to be useable.<ref name=bsp/> Corona-style mills are generally low-quality products (e.g. they may add metal shavings to the grist). Buy pre-milled grain until you're ready to invest in a roller mill. | |||
== Mounting the mill == | |||
It is important to set up the mill on a base to keep the frames aligned properly. If the frames aren't straight, the rollers may bind.<ref>[https://www.monsterbrewinghardware.com/store/pc/catalog/MM-2-3-20Instructions.pdf "Monster Mill MM 2/3/PRO Instructions."] Monster Brewing Hardware, 2015.</ref> As you are securing it to the base, make sure all the rollers spin freely. Most mills either come with a base or have one available. These bases are typically designed to let the mill sit on top of a plastic bucket, and this setup is fine in most cases. However if you are adding a dedicated motor, it will be necessary to attach the mill to a larger base or table. | |||
Monster Mill accessories like {{Amazon|B0064OMA04|this base}} will also work for the Kegco 3-roller mill. | |||
== Driving the mill == | |||
Three options exist for powering the mill. Any of these options can produce a good crush, so the choice of power just depends on your personal preference and budget. Warning: We do not recommend [https://www.homebrewtalk.com/threads/motorize-grain-mill-will-a-drill.403217/post-5086940 driving the mill with a hamster]. | |||
# Hand crank | |||
# Electric drill | |||
# Electric non-drill motor | |||
=== Hand crank === | |||
A hand crank is available for many models, and attaches to the drive shaft with a screw. It is operated by turning the crank handle. This may get tiring for milling large amounts of grain. | |||
=== | === Electric drill === | ||
[[File: | [[File:Milling-drill.png|thumb|Driving the mill with a cordless drill. Photo by Rob Stein.]] | ||
For most home brewers a drill is the preferred method to drive a mill. It is easier to set up and more economical than using a non-drill motor, and significantly less laborious than hand cranking. Low RPM drills provide the best torque. We don't recommend using an external speed limiter ({{Amazon|B00U3LD1WA|example}}) on a high RPM drill because they significantly reduce the torque.<ref>[https://www.homebrewtalk.com/threads/speed-controller-for-corded-drill-used-for-milling-grain.629645/ Speed controller for corded drill, used for milling grain?] Homebrew Talk website. 2017. Accessed 2020.</ref><ref>[https://www.homebrewersassociation.org/forum/index.php?topic=23703 Monster mill drill question.] American Homebrewers Association website. 2015. Accessed 2020.</ref> Affixing a zip tie, 2" tri-clamp, or U-bolt to the trigger of a variable speed drill can help control and maintain a constant speed. A corded drill is generally more powerful than a cordless one, and will usually last longer. However cordless drills can also work well.<ref>[https://www.beeradvocate.com/community/threads/need-drill-recommendations.581479/ Need drill recommendations.] BeerAdvocate website. 2018. Accessed 2020.</ref><ref>[https://www.homebrewersassociation.org/forum/index.php?topic=9367 Proper drill for milling grain.] American Homebrewers Association website. 2011. Accessed 2020.</ref> The one requirement to using a drill is that the drill chuck fits onto the mill drive shaft (which range from 3/8" to 1/2" [9-12mm]). If you are holding the drill while milling, you must also hold down the base of the mill. Otherwise the torque may cause the mill to flip over, causing damage to equipment and/or personal injury. | |||
{| class="wikitable" | |||
|+ Recommended Products | |||
|[https://www.harborfreight.com/power-tools/drills-drivers/drill-mixers/75-amp-12-in-low-speed-spade-handle-drillmixer-56179.html Bauer corded drill from Harbor Freight] || 1/2" chuck, 0-600 rpm, variable speed. These are tried and true, and are frequently recommended by home brewers due to the low cost. | |||
|- | |||
|{{Amazon|B086K5Q6JG|Greenworks 24V cordless drill (Amazon)}} || 1/2" chuck, 0-380 rpm (also has higher speed setting), variable speed, brushless. | |||
|} | |||
=== Non-drill motor === | |||
Some brewers prefer using a dedicated non-drill motor. See [[Motorizing a mill]]. | |||
=== Reducing torque requirement === | |||
If your drill/motor is having issues with stalling, or you'd like to reduce the load on it in order to extend its life, or you are wanting an easier job of hand cranking, you can reduce the amount of torque needed to drive the mill by reducing the amount of grain feeding into the rollers. All you need to do is create and affix cardboard inserts into the bottom of the hopper. | |||
<gallery widths=300px heights=300px mode="nolines"> | |||
File:Mill-tabs.jpg | |||
File:Roller-mill-flow-limiting2.jpg | |||
File:Torque-barrier.png | |||
File:Clear-flow-limiters.png | |||
</gallery> | |||
==Setting the gap== | |||
[[File:Angled-feeler-gauge.png|thumb|An angled feeler gauge for measuring the roller gap on a 3-roller mill. Photo by Dr. Adam Bittner]] | |||
All of the mills we recommend have an adjustable roller gap. A tighter gap produces smaller grain particles, called a fine crush, and a larger gap creates a coarse crush. '''There is not a one-size-fits-all gap setting.''' The ideal mill gap setting is dependent on your mill, your brewing system, and factors related to the grain (which can vary even from batch to batch and with storage time).<ref name=Kunze/><ref name=Crescenzi>Crescenzi AM. [https://onlinelibrary.wiley.com/doi/abs/10.1002/j.2050-0416.1987.tb04498.x Factors governing the milling of malt.] ''J Inst Brew.'' 1987;93:193–201.</ref><ref name=delucchi>Delucchi V. [https://byo.com/article/the-perfect-crush/ The perfect crush.] Brew Your Own website. 2019. Accessed January 2021.</ref> For each batch, the objective is to find an acceptable middle ground between lautering/recirculation effectiveness, [[efficiency]] (yield), and quality.<ref name="Briess">Hansen B. [https://web.archive.org/web/20190712061433/https://www.brewingwithbriess.com/Assets/Presentations/Briess_2007CBC_Practical_Milling.ppt Practical milling for the craft brewer.] Briess Malt & Ingredients Co. 2007. Accessed 2020.</ref><ref name=smart3>Holbrook CJ. Brewhouse operations. In: Smart C, ed. [[Library|''The Craft Brewing Handbook.'']] Woodhead Publishing; 2019.</ref> Some experimentation with different settings is needed to find out what works best for your mill and your brewing system, although there is a wide range that will be adequate.<ref>[http://www.themodernbrewhouse.com/forum/viewtopic.php?f=2&t=1795 Mashing for high gelatinisation temps.] The Modern Brewhouse website. 2020. Accessed 2020.</ref> Also, the grist should be visually monitored every milling to ensure it is being properly crushed. | |||
The gap | There are two main things to consider when experimenting with the roller gap: | ||
# The gap must be small enough so that all the kernels are crushed, which helps to maximize efficiency. This can easily be verified by milling about a cup of grain and visually inspecting it (carefully sort through it looking for uncrushed kernels).<ref name=pro/> | |||
# The gap must be large enough to avoid problems with a [[stuck mash]] or slow lautering/recirculation.<ref name=bsp/><ref name=pro>Miller D. [http://brewlikeapro.net/maltmilling.html Mills and milling.] Brew Like A Pro website. 2012. Accessed 2020.</ref><ref name=kuhbeck>Kühbeck F, Dickel T, Krottenthaler M, et al. | |||
[https://onlinelibrary.wiley.com/doi/pdf/10.1002/j.2050-0416.2005.tb00690.x Effects of mashing parameters on mash β-glucan, FAN and soluble extract levels.] ''J Inst Brew.'' 2005;111(3):316–327.</ref><ref name=kall>Kallmeyer M. [https://draymans.com/to-mash-or-not-to-mash-kurzhoch/ To mash or not to mash Kurz/Hoch.] Drayman's Brewery website. 2016. Accessed online March 2024.</ref> This greatly depends on your system/process, and experimentation is required to find the smallest acceptable gap. For example, a simple BIAB system can tolerate a fine crush, whereas a recirculating system tends to benefit from more intact husks. Keep in mind that excessive husk damage can potentially affect beer quality (see below).<ref name=Mousia/> Also be aware that 2-roller mills have a lower limit at which the rollers can feed the grain. | |||
For most systems, a gap in the range of 0.025" to 0.050" (0.7–1.2mm) is appropriate.<ref name="LOB-1069"/><ref>[http://www.themodernbrewhouse.com/forum/viewtopic.php?f=4&t=697 Dry crush mill gap.] The Modern Brewhouse website. 2018. Accessed 2020.</ref> To measure this, a feeler gauge (which is a stack of metal pieces with different marked thicknesses) can be inserted into a gap to precisely measure it. To achieve gaps that are not the same as a single blade, stack multiple blades together to add up to the gap you want to set. In a pinch, a standard credit card can be used to set a 0.030" (0.76mm) gap.<ref>[https://en.wikipedia.org/wiki/ISO/IEC_7810 "ISO/IEC 7810."] Wikipedia. Accessed May 2020.</ref> If you have a 3-roller mill, an angled feeler gauge should be used because a straight feeler gauge cannot access the adjustable gap while the mill is assembled. | |||
{| class=wikitable | |||
|+Recommended products | |||
|- | |||
|{{Amazon|B07B3TQQSV|Straight feeler gauge (Amazon)}} || Blades range from 0.001" to 0.040" (0.03mm to 1mm) | |||
|- | |||
|{{Amazon|B004FEPDJU|Angled feeler gauge (Amazon)}} || Blades range from 0.005" to 0.020" (0.127mm to 0.508 mm) | |||
|} | |||
[[File:Gap-markings.jpg|thumb|right|Gap settings marked by the adjustment knobs]] | |||
Process: | |||
# Insert the gauge into a loose gap and then gently tighten the rollers on it. The blades should go into the gap between the rollers with a minimum amount of force, and should not be crushed in the gap. Adjust the gap on both ends of the roller to be the same.<ref name=monster/><ref>Ream J. [http://www.homebrewengineer.com/adjust-mill-gap-barley-crusher/ How to: adjust the mill gap of a barley crusher.] Homebrew Engineer blog. 2015. Accessed 2020.</ref> | |||
# On mills with adjustment knobs, mark on the frame what the gap is at the a variety of knob positions. This allows you to repeat different gap settings without needing the feeler gauge again. We suggest marking increments every 0.005" (0.1mm) over a range of 0.020" to 0.055" (0.5–1.4mm). | |||
== Milling considerations == | |||
Several things should be considered when deciding on mill gap and other parameters that will affect grist performance during [[mashing]]. | |||
=== Husk integrity === | |||
Pulverizing the entire grain into flour should generally be avoided.<ref name="Szwajgier">Szwajgier D. [https://onlinelibrary.wiley.com/doi/pdf/10.1002/j.2050-0416.2011.tb00505.x Dry and wet milling of malt. A preliminary study comparing fermentable sugar, total protein, total phenolics and the ferulic acid content in non-hopped worts.] ''J Inst Brew.'' 2011;117(4):569–577.</ref><ref name=Warpala>Warpala IWS, Pandiella SS. [https://www.sciencedirect.com/science/article/abs/pii/S0960308500701982 Grist fractionation and starch modification during the milling of malt.] ''Food and Bioproducts Processing.'' 2000;78(2):85–89.</ref><ref name=kall/> A high percentage of flour will increase the viscosity of the wort, increasing the likelihood of the dreaded "stuck mash" or slow recirculating and lautering. We want the husks to be as intact as possible, not only for filtering, but also because finely shredded husks can cause astringent, bitter, or harsh off flavors.<ref name=mostra/><ref name="Szwajgier"/><ref>[https://www.winning-homebrew.com/homebrew-grain-mills.html Homebrew grain mills and a pictorial guide to milling grain.] Winning-Homebrew.com website. Accessed May 2020.</ref><ref name=brewer>Whitting C. [https://www.beerandbrewer.com/milling-your-grain/ "Milling Your Grain."] Beer & Brewer. 2018. Accessed 2020.</ref><ref name=more>Brown R. [https://www.morebeer.com/articles/DIY_Homebrew_Grain_Mill Homemade grain milling systems.] MoreBeer. Accessed May 2020.</ref><ref name=adb>Narziss L, Back W, Gastl M, Zarnkow M. [[Library|''Abriss der Bierbrauerei.'']] 8th ed. Weinheim, Germany: Wiley-VCH Verlag GmbH & Co. KGaA; 2017:126–130.</ref><ref name=fix>Fix G. [[Library|''Principles of Brewing Science.'']] 2nd ed. Brewers Publications; 1999.</ref> Excessive milling promotes the extraction and solubilization of undesirable compounds into the wort and beer, such as [[silicates]], [[fatty acids|lipids]], husk-derived tannins ([[phenolic compounds]]), and large-molecular [[protein]]s, which can cause excess formation of [[trub]], deposits, color changes, [[haze]]s, and a shorter shelf life.<ref name=Kunze/><ref>Zepf M. [https://beerandbrewing.com/dictionary/VWpGLEPUS6/ Milling.] Craft Beer & Brewing. Accessed May 2020.</ref><ref>Siebert KJ. [https://www.sciencedirect.com/science/article/pii/S0023643806000259 Haze formation in beverages.] ''Lebenson Wiss Technol.'' 2006;39(9);987–994.</ref><ref name=Szwajgier/><ref name=Moura>Pereira de Moura F, Rocha dos Santos Mathias T. [https://www.mdpi.com/2306-5710/4/3/51/pdf A comparative study of dry and wet milling of barley malt and its influence on granulometry and wort composition.] ''Beverages.'' 2018;4(51).</ref><ref name=golston/><ref name=pre>Prechtl C. [https://www.mbaa.com/publications/tq/tqPastIssues/1967/Abstracts/tq67ab16.htm Some practical observations concerning grain bitterness in beers and its amelioration.] ''Tech Q Master Brew Assoc Am.'' 1967;4(1):98–103.</ref> Lastly, too much husk flour can potentially result in loss of [[extract]] because starch will be adsorbed to the husk and discarded with it.<ref name=esslinger>Krottenthaler M, Back W, Zarnkow M. Wort production. In: Esslinger HM, ed. [[Library|''Handbook of Brewing: Processes, Technology, Markets.'']] Weinheim, Germany: Wiley-VCH Verlag GmbH & Co. KGaA; 2009.</ref> | |||
However, fine milling does not ''necessarily'' cause extraction of harsh flavors, and it can be acceptable depending on the [[lautering]] method.<ref name=bsp>Briggs DE, Boulton CA, Brookes PA, Stevens R. [[Library|''Brewing Science and Practice.'']] Woodhead Publishing Limited and CRC Press LLC; 2004.</ref><ref name=derouck>De Rouck G, Jaskula-Goiris B, De Causmaecker B, et al. [https://www.brewingscience.de/index.php?tpl=table_of_contents&year=2013&edition=0001%252F0002&article=82374 The impact of wort production on the flavour quality and stability of pale lager beer.] ''BrewingScience.'' 2013;66(1/2):1–11.</ref> [[brewing pH|Mash pH]] strongly influences the extraction of negative compounds, which can be particularly troublesome when [[Sparging|fly sparging]]. Therefore the issue of undesirable flavor extraction from pulverized husks may be less worrisome for home brewers who properly control mash and sparge pH, although husk pulverization may still lead to other issues such as haze and excessive trub depending on other factors.<ref>De Rouck G, Jaskula B, De Causmaecker B, et al. [https://www.tandfonline.com/doi/abs/10.1094/ASBCJ-2013-0113-01 The influence of very thick and fast mashing conditions on wort composition.] ''J Am Soc Brew Chem.'' 2013;71(1):1–14.</ref> | |||
Husk integrity can be improved by conditioning the grain, using an appropriately large mill gap, and using a 3-roller mill or a mill with fluted rollers. | |||
=== Milling speed === | |||
In general, a milling speed between 50–300 RPM is considered appropriate for small scale milling.<ref name="lob271"/><ref name="LOB-1069"/><ref name="monster"/> Be aware that it usually takes a little more torque to get the mill going. If your drive method is struggling, use the method to reduce torque described above. | |||
Some home brewers have found that milling at a lower speed reduces damage to husks.<ref name=lob993/><ref name=lob271>[http://www.themodernbrewhouse.com/forum/viewtopic.php?f=2&t=271 Conditioned grain mill gap.] The Modern Brewhouse website. 2017–2018. Accessed 2020.</ref><ref>[https://www.homebrewtalk.com/threads/so-what%E2%80%99s-the-right-harbor-freight-drill-for-a-mill-20-off-coupon-out-now.673941/ So what's the right Harbor Freight drill for a mill? 20% off coupon out now.] Homebrew Talk website. 2020. Accessed 2020.</ref><ref>[https://www.homebrewtalk.com/threads/best-place-to-get-a-grain-mill.700592/post-9272893 Best place to get a grain mill.] Homebrew Talk website. 2022. Accessed May 27, 2022.</ref> Other brewers have not noticed a significant effect of milling speed on the grist (appearance or granulometry),<ref>[http://www.themodernbrewhouse.com/forum/viewtopic.php?f=11&t=1929 Milling test results.] The Modern Brewhouse website. 2020. Accessed July 2020.</ref><ref name=bittner/> which is in agreement with professional literature.<ref name=Warpala/><ref name=Mousia/> | |||
=== Oxidation === | |||
[[File:Mill-on-cooler.jpg|thumb|right|Mill with base on top of a cooler mash tun]] | |||
The grist begins to [[Oxidation|oxidize]] immediately upon milling (because the inside of the kernels are then exposed to air and moisture) and this can have a negative impact on the subsequent beer quality.<ref name=Kunze/><ref name=adb/><ref name=pasame>Pascoe HM, Ames JM, Chandra S. [https://www.tandfonline.com/doi/abs/10.1094/ASBCJ-61-0203 Critical stages of the brewing process for changes in antioxidant activity and levels of phenolic compounds in ale.] ''J Am Soc Brew Chem.'' 2003;61(4):203–209.</ref><ref name=cheyni>Cheynier V. [https://www.sciencedirect.com/science/article/pii/S0002916523275115 Polyphenols in foods are more complex than often thought.] ''Am J Clin Nutr.'' 2005;81(1):223S–229S.</ref> Therefore the time between milling and dough-in should be kept as short as possible.<ref name=golston>Golston AM. [https://www.mbaa.com/publications/tq/tqPastIssues/2021/Pages/TQ-58-1-0322-01.aspx The impact of barley lipids on the brewing process and final beer quality: A mini-review.] ''Tech Q Master Brew Assoc Am.'' 2021;58(1):43–51.</ref> | |||
Modern commercial low oxygen breweries fill all areas containing milled grain with inert gas (CO<sub>2</sub> or N<sub>2</sub>) to prevent oxygen exposure.<ref name=Kunze/><ref name=bsp/><ref name=adb/><ref name=derouck/><ref name=golston/> Brewers looking to [[low oxygen brewing|preserve fresh grain flavor]] may do this simply by flowing inert gas into the bottom of the mash tun and milling directly into it, or by flushing the grist with inert gas after milling.<ref name=stephenson>Stephenson WH, Biawa JP, Miracle RE, Bamforth CW. [https://onlinelibrary.wiley.com/doi/pdf/10.1002/j.2050-0416.2003.tb00168.x Laboratory-scale studies of the impact of oxygen on mashing.] ''J Inst Brew.'' 2003;109(3):273–283.</ref><ref name=mullerr>Muller R. [https://www.tandfonline.com/doi/abs/10.1094/ASBCJ-53-0053 Use of 5,5’-dithiobis (2-nitrobenzoic acid) as a measure of oxidation during mashing.] ''J Am Soc Brew Chem.'' 1995;53(2):53–58.</ref><ref>[http://www.themodernbrewhouse.com/forum/viewtopic.php?f=2&t=1025 CO2 purge of mash tun prior to underletting?] The Modern Brewhouse website. 2018. Accessed 2020.</ref><ref name="lob1394">[http://www.themodernbrewhouse.com/forum/viewtopic.php?f=18&t=1394 Milling into mash tun.] The Modern Brewhouse website. 2019. Accessed 2020.</ref> Purging a mostly covered mash tun at 1–2 psi for about 10 minutes has been shown to effectively remove the vast majority of oxygen in the vessel.<ref>[http://www.themodernbrewhouse.com/forum/viewtopic.php?f=11&t=751 Purging grist in the tun.] The Modern Brewhouse website. 2018. Accessed 2020.</ref> A regulator may start to freeze up and/or significantly chill the mash tun parts, causing dough-in temperature to be too low. A fix for that is to get a cheap heat lamp or hair dryer and point it at your regulator.<ref name="lob1394"/> Dry ice can also be used to purge: put the dry ice in a jar with water and connect it with tubing to the mash tun. Note that flushing with inert gas during the actual milling process appears not to be critical, as oxidation does not occur immediately (at least with regard to [[lipids]] or [[protein]]s).<ref name=wackerbauer>Wackerbauer K, Meyna S, Marre S. [http://themodernbrewhouse.com/wp-content/uploads/2017/04/174-178.pdf Hydroxy fatty acids as indicators for ageing and the influence of oxygen in the brewhouse on the flavour stability of beer.] ''Monatsschrift Brauwiss.'' 2003;56(9/10):174–178.</ref><ref name=mullerr/> | |||
The | === Grain moisture === | ||
The moisture content of the malt influences the fineness of the grist. Moisture makes the grain more elastic and the crush becomes more coarse. Coarse particles adhering to the husks are more difficult to degrade during the mashing process, leading to a lower yield. This mainly applies to malts which, if improperly stored, have a water content of 8–12%. Unlike with grain conditioning, this moisture is distributed through the entire grain. On the other hand, a malt with very little moisture has a tendency to be crushed too fine, destroying the husks and increasing the flour content. This may occur when very young dark malts are used, which is probably an unlikely situation for home brewers. Conditioning may help avoid problems in both of these cases, although minimizing moisture during [[grain]] storage is still a high priority.<ref name=adb/> | |||
=== Specialty grains === | |||
Lighter color kilned or dry roasted specialty malts will crush like base malts, while caramel/crystal and extremely dark roasted products are more brittle and tend to shatter rather than crush. Malts that shatter tend to create more flour which can contribute to difficulties during [[lautering]]. The fine particles can fill in the spaces in the otherwise permeable bed causing a slowed or stuck lauter. These brittle specialty malts can typically be milled with a wider mill gap resulting in a larger particle size that will still allow for complete flavor and aroma extraction which is the primary function of these malts. Finding the balance of desired particle size starts with adjusting the mill gaps.<ref>Geurts J. [http://blog.brewingwithbriess.com/9-5-grind/ 9-5 grind.] Briess blog. 2018. Accessed 2020.</ref> | |||
'''Wheat, rye, and oats'''<br/> | |||
Generally speaking, these grains have smaller kernels (especially rye)<ref name=smart1>Howe S. Raw materials. In: Smart C, ed. [[Library|''The Craft Brewing Handbook.'']] Woodhead Publishing; 2019.</ref> and are harder than barely. Therefore the mill gap may need to be decreased when milling these grains, and more torque may be required while milling. Mill small samples to check for whole kernels, just as we suggested above for setting the gap for barley. Take note of the ideal gap for each grain. | |||
'''Things that don't need to be milled'''<br/> | |||
* "Flaked" or "rolled" grain [[adjuncts]] do not need to be milled, although they can be run through the mill with the rest of the grain if it is convenient.<ref>[http://www.brewingwithbriess.com/Assets/PDFs/Briess_PISB_BrewersBarleyFlakes.pdf Brewers barley flakes.] Briess Product Information Sheet. 2019. Accessed 2020.</ref> | |||
* Rice hulls should not be put through the mill because their whole purpose is to remain intact in order to aid filtering. | |||
* Most home brew mills are not suitable for milling corn. | |||
* Fingers, clothing, rocks, or bits of metal should not be milled. Please be careful, especially when using power tools. | |||
== | === Dust === | ||
To avoid excessive dust contaminating your gear and wort, it's considered prudent to mill away from your cold-side gear and away from where you'll be chilling and fermenting your wort, particularly if you do not condition the grain. Conditioning can help lower the amount of dust generated while milling. However, dust can still be created when measuring the grain. Wearing a mask can be beneficial for your health since breathing in grain dust is not so great.<ref name=mostra/> Thanks to COVID-19 you do have a mask, right? | |||
http://www. | ==Conditioning the grain== | ||
[[File:Unmilled-grain.jpg|thumb|Simple grain conditioning setup]] | |||
Dry husks fragment easily, which may cause issues (see above). Husks become more elastic when they are moist, making them easier to protect.<ref name=Kunze/><ref>Rabe B. [http://www.themodernbrewhouse.com/uncategorized/grain-conditioning/ Grain Conditioning.] The Modern Brewhouse website. 2016. Accessed 2020.</ref><ref name=LOB-1069/><ref name=lob993/><ref>Venturini Filho WG, Nojimoto T. [https://www.scielo.br/scielo.php?pid=S0101-20611999000200003&script=sci_arttext Utilization of the wet milling malt steep water as raw material on brewing.] ''Ciênc Tecnol Aliment.'' 1999;19(2):174-178.</ref><ref name=Crescenzi/><ref name=bsp/><ref name=hob11/> Increasing the moisture content of the grain husk right before milling is called "conditioning". The goal is to increase it just enough to minimize shredding as the grain passes through the mill. Generally the amount of water added should be about 1–2% of the weight of grain.<ref name=adb/><ref name=Kunze/><ref name=Szwajgier/><ref name=esslinger/> It's important not to add too much water because our mills cannot process wet grain; it will stick to the rollers. The recommended amount of moisture is low enough that the grain should not be sticky and it will not cause rollers to rust. Wheat malt also benefits from conditioning even though it is huskless.<ref name=Kai>Troester K. [http://braukaiser.com/wiki/index.php?title=Malt_Conditioning Malt Conditioning.] German brewing and more wiki. Updated 2009. Accessed 2020.</ref> | |||
Conditioning is not a necessary step, but it does have advantages when combined with a proper roller gap.<ref name=Szwajgier/> The roller gap may need to be (and probably should be) tightened when conditioning, to make sure all the grains get crushed and to reap the benefits of more finely crushed starch.<ref name=lob1167>[http://www.themodernbrewhouse.com/forum/viewtopic.php?f=2&t=1167 Seriously bad mash efficiency suddenly!] The Modern Brewhouse website. 2019. Accessed 2020.</ref><ref name=Crescenzi/><ref name=bsp/> Basically all modern commercial German breweries that use lauter tuns (as opposed to mash filters) either condition their malt or mill it wet.<ref name=Kai/> | |||
Advantages: | Advantages: | ||
* | * Dust is reduced during milling.<ref name=lob993/><ref name=mashing/> | ||
* The risk of [[dough balls]] is decreased.<ref name=lob993>[http://www.themodernbrewhouse.com/forum/viewtopic.php?f=2&t=993 Revisiting grain conditioning.] The Modern Brewhouse website. 2018–2019. Accessed 2020.</ref> | |||
* | * The rollers may grip the grain better and feed faster.<ref name="lob993"/> | ||
* Improved husk integrity provides a looser grain bed and easier lautering.<ref name="Kunze"/><ref name="Szwajgier"/><ref name=bsp/><ref name=mashing/> | |||
* More intact husks means that the grain can be ground more thoroughly (tighter gap) without affecting lautering.<ref name="Kunze"/><ref name="Szwajgier"/><ref name=bsp/><ref name=adb/> | |||
* A tighter gap means that the starch is crushed more thoroughly. | |||
* More thoroughly crushed starch means that [[efficiency]] and [[attenuation]] are increased and [[conversion]] is faster.<ref name="Kunze"/><ref name=adb/><ref name=bsp/> | |||
* Reduced husk damage can have quality benefits on the resulting beer. (See above) | |||
* | * Manually stirring and looking at your grain allows you to find any rocks, metal pieces, or other foreign objects that may be mixed with the grain and could otherwise damage your mill. | ||
Disadvantages: | |||
* Additional time and labor is required. | |||
* Milling may require additional torque. | |||
* A roller gap adjustment is probably needed to optimize crush (and prevent uncrushed kernels).<ref name=bsp/> | |||
* Protein extraction may be higher.<ref name="Szwajgier"/> | |||
'''Conditioning Method 1''' (Editor's Choice)<ref name="lob993"/> | |||
# Put the grain into a wide plastic tub. | |||
# Add water to a small spray bottle. | |||
# Spray the grain evenly while stirring (e.g. with your hand or a mash paddle) until the grain becomes pliable. | |||
# The grain may be milled about 10 minutes after wetting. | |||
View this method in action: | |||
{{#ev:youtube|https://www.youtube.com/watch?v=rSAG31iTjK0|||||start=375}} | |||
'''Conditioning Method 2''' (no stirring)<ref name="LOB-1069"/> | |||
# Weigh out the grain in buckets. | |||
# Add water to a small spray bottle. | |||
# Pour a thin layer into a wide plastic tub. | |||
# Spray it with water from a spray bottle. | |||
# Repeat steps 3 & 4 until done. | |||
# The grain may be milled about 10 minutes after wetting. | |||
= | '''Conditioning Method 3''' (sink sprayer)<ref name="LOB-1069"/> | ||
# Put the grain into a wide plastic tub. | |||
# Attach a flexible misting nozzle to a sink hose. | |||
# Spray the grain evenly while stirring (e.g. with your hand or a mash paddle) until the grain becomes pliable. | |||
# The grain may be milled about 10 minutes after wetting. | |||
If you are using a disc mill (like a Corona/Victoria style mill) instead of a roller mill, different amounts of moisture can possibly have variable and unpredictable effects on the resulting crush.<ref name="Moura"/> Therefore we cannot recommend conditioning when using such a mill, but you may still experiment if you wish. | |||
For images comparing conditioned vs unconditioned grist, see here: [http://www.themodernbrewhouse.com/uncategorized/grain-conditioning/ Grain Conditioning at LOB.] and [http://braukaiser.com/wiki/index.php?title=Malt_Conditioning Malt Conditioning at German Brewing]. | |||
==Cleaning and maintenance== | |||
[[File:Mill-body-end-plates.jpg|thumb|right|Left: dirty end plate. Right: clean end plate]] | |||
'''First time cleaning:''' After adjusting the gap, mill about a pound of grain and then throw that away. This removes the machine oils from the rollers. | |||
'''Cleaning after use:''' A paintbrush and compressed air will remove dust and any grain and dust clinging to the rollers. A stainless steel brush can help remove stubborn particles. | |||
'''Removing and preventing rust:''' Most mills have hardened steel rollers, so it is possible for them to rust. Running about a pound of grain or rice through the mill may be all that's needed to remove rust from the rollers. If that doesn't work, brush the affected area with a stainless steel brush until the rust is gone. Dust attracts moisture, so keeping the mill clean as described above will help prevent the rollers from rusting,<ref name=bsp/> as will storing the mill in a dry location. If you condition your grain, consider reserving a half pound of unconditioned grain to mill at the end to remove any moisture. | |||
'''Maintenance:''' The mills we recommend are fairly maintenance-free, particularly if you have one with sealed ball bearings and if you clean the rollers after use. However, mills (especially those with bronze bushings in particular) may benefit from periodic cleaning: disassemble, wipe clean, and lubricate. Visually check the gap setting before milling to make sure the adjustable gap is not slipping and that the rollers are in proper alignment. Rollers out of alignment may bind. Rollers with stubborn grain stuck between the knurling can be cleaned with a short (e.g. 30 minute) hot alkaline bath (see [[cleaning]]), although some rust will likely need to be removed afterwards. | |||
{| class=wikitable | |||
|+Suggested cleaning and maintenance products | |||
|- | |||
|Stainless steel brush||{{Amazon|B000CFLET4}} | |||
|- | |||
|Food-grade machine oil for lubrication||{{Amazon|B0013J62O0}} | |||
|} | |||
==Sieve testing== | |||
[[File:Sieves-with-grain.png|thumb|Sieves with grain sample. Photo by Dr. Adam Bittner.]] | |||
Sieves can be used to scientifically measure the particle sizes of the grist. This is called granulometry, or sieve testing. Unfortunately, the sieves are a bit expensive and the testing process is somewhat labor-intensive. Furthermore, the results are borderline useless since the crush produced by home brew mills differs greatly from that of a commercial mill, even with similar granulometry results.<ref name=bittner>Bittner A. [[User_blog:Adam/Think_like_a_scientist:_Sieve_testing|Think like a scientist: Sieve testing.]] Brewing Forward website. 2021. Accessed February 2021.</ref> Therefore, we do not recommend home brewers invest in the materials or effort required for sieve testing. | |||
Our recommendation notwithstanding, sieve testing can be used in combination with visual inspection to compare how different milling parameters can affect the crush, and it can be helpful to maintain a tight degree of consistency through periodic testing. Large breweries use a machine to conduct the test, but it can also be done by hand using a standardized protocol, which has been shown to produce satisfactory results.<ref>[https://doi.org/10.1094/ASBCJ-61-0246 Malt grist by manual sieve test.] ''J Am Soc Brew Chem.'' 2003;61(4):246–249.</ref><ref>Schwarz P, Barr J, Joyce M, Power J, Horsley R. [https://www.tandfonline.com/doi/abs/10.1094/ASBCJ-60-0010?src=recsys Analysis of malt grist by manual sieve test.] ''J Am Soc Brew Chem.'' 2002;60(1):10–13.</ref> See [[Sieve testing]] for more information. | |||
==See also== | |||
*[[Grain]] | |||
*[[Malt]] | |||
*[[Mashing]] | |||
External links: | |||
*https:// | * [https://www.youtube.com/watch?v=_HUHdUiy6Js Video from Integrity Homebrewing] comparing the effects of different mill gaps, mill speeds, and grain conditioning (20 minute video) | ||
*http://brewlikeapro.net/maltmilling.html | *[http://brewlikeapro.net/maltmilling.html Mills and Milling] by Dave Miller, author of ''Brew Like A Pro'' | ||
* | *If you're really into DIY: [https://www.morebeer.com/articles/DIY_Homebrew_Grain_Mill?a_aid=ModernBrewhouse Suggestions to help build a mill from scratch] | ||
==References== | ==References== |
Latest revision as of 20:43, 15 May 2024

Grain consists mainly of starch granules (endosperm) inside a husk. Before the mash, grain must be mechanically crushed using a mill. The crushing process breaks open the husks, exposing the starch, and also cracks the starch into smaller bits, increasing the surface area exposed to water and enzymes during mashing.[1] The crushed grain is referred to as grist. In general, the crush quality affects the mashing process, including saccharification time, lautering, efficiency, fermentation, as well as the color, taste, and overall character of the beer.[2][3]
Milling Process Overview:
- Weigh the grain on a scale per the recipe specifications.
- Condition the grain (optional)
- Crush the grain by adding it to the hopper and spinning the drive roller. The grist must be collected in a bucket or milled directly into the mash vessel.
- Verify the crush by visual inspection. It's generally a good idea to inspect the first handful of grain before continuing with the rest.
Grain mills[edit]
Why own a mill?
- Freshness - Milling immediately before brewing results in the freshest malt possible (helping to avoid oxidation).
- Control - Adjusting the gap allows you to tailor the crush to your own system and maximize efficiency.
- Consistency - The crush size may be inconsistent with pre-milled grain.
- Grain conditioning - Milling on site gives you the option to condition your grain (see below).
- Cost savings - A personal grain mill eventually pays for itself because A) you avoid a milling fee and B) you can buy grain in bulk.
Features[edit]

- 3-roller vs 2-roller - In a 3-roller mill, the grain is pre-crushed in the gap between the top two rollers, and then the grain flows into the gap between the drive roller and bottom roller, crushing it further. The top gap is fixed at around 0.060–0.070" which easily pulls in both wheat and barley, providing superior feed, and softening the starch without tearing up the husk.[4] The lowered husk damage aids in lautering among other things (see below). The double crush also more fully separates the husk from the starch. The downsides to 3-roller mills are that more power (torque) is typically required to drive them and they are generally more expensive. 2-roller mills are more budget friendly.
- Bearings vs bushings - Sealed ball bearings generally require no maintenance and can have a significantly longer lifespan than bushings, particularly if you drive the mill with a pulley.[5][6][7][8] On the other hand, bushings have more friction and may wear over time, such that they will need to be replaced at some point.[9][10] Therefore we recommend a mill with sealed ball bearings. However, bushings are still an acceptable option when using a direct drive system such as a drill. Bushings may benefit from periodic cleaning and lubrication with a drop of food-grade mineral oil; check with the manufacturer.[11][12]
- Roller material - For most brewers, hardened steel is the best option for roller material due to its durability.[13] However, stainless steel has better protection against corrosion (although it is also more expensive). If you live in a damp or coastal region, stainless might be a good option.[14]
- Roller diameter - Larger diameter helps the grain feed through the rollers.[2][15]
- Knurled vs fluted rollers - Roller morphology has an important effect on the crush by reducing damage to the husk. Modern commercial mills always have fluted rollers.[3][2][16] On the other hand, most home brew mills have rollers with a diamond knurling pattern, which is necessary to improve the grain feed through small diameter rollers. A few home brew mills with relatively larger rollers (e.g. MattMill and Ss Brewtech) have a fluted morphology. However, the fluting pattern on these is completely different than commercial mills,[2] so it is unclear whether the fluting provides any benefit over knurling for home milling.
- Drive shaft - A 1/2" integrated drive shaft is the most durable. If you have a drill that you plan to use for milling, verify that it can fit on the drive shaft for the mill you want to purchase. (See Driving the mill below)
- Hopper size - Hopper size is a matter of convenience and budget. It is most convenient to add the grain to the hopper all at once, however it doesn't hurt anything if you need to pause partway through milling in order to fill the hopper with more grain. Portability, weight, and storage space should be also be taken into account. Some mills have optional hopper extensions to purchase, or you can make a hopper extension yourself.
- Throughput rate - Differences in roller length and how fast the rollers feed grain is generally negligible for home brewers and not something that needs to be considered. Throughput depends largely on drive speed (RPM) and not the particular mill characteristics.
- Roller speed differential - Modern large-scale commercial mills have the rollers spinning at different speeds.[2] This increases the effectiveness of the crush by shearing off the husk from the endosperm, which serves to increase yield while reducing husk damage.[3] The only home brew mill with speed differential is from Ss Brewtech.
Best mills available[edit]
2-Roller Mills | ||||
---|---|---|---|---|
Mill | Rollers | Bearing type | Accessories | Where to purchase |
![]() Kegco 2, Hullwrecker, Malt Muncher 2 (All the same) |
Knurled 1.25" x 5" hardened steel | Sealed ball bearings | Includes 7lb hopper and hand crank |
|
Monster Mill 2 | Knurled 1.5" x 6" hardened steel or stainless steel optional | Bronze bushings | 11lb hopper, hopper extension, hand crank, and base are all optional. | |
MattMill Kompakt | Fluted 2.75" x 2" hardened steel | Roller bearings[17] | Hand crank and base are optional and hopper is generally DIY. | |
3-Roller Mills | ||||
Mill | Rollers | Bearing type | Accessories | Where to purchase |
![]() Malt Muncher 3 (same) |
Knurled 1.5" x 6" hardened steel | Sealed ball bearings | Includes 12lb hopper and hand crank. Base is optional. |
|
Monster Mill 3 | Knurled 1.5" x 6" hardened steel or stainless steel optional | Bronze bushings | 11lb hopper, hopper extension, base, and hand crank are all optional. | |
Premium Motorized Mills | ||||
Mill | Rollers | Bearing type | Accessories | Where to purchase |
Ss Brewtech | Fluted 4" diameter stainless steel, with speed differential | Sealed ball bearings | Includes motor and 25lb hopper. Base/cart is optional. | |
MoreBeer UltiMill | Knurled 2" diameter hardened steel | Unknown | Includes 60lb hopper with lid, motor, and stand. |
Crankandstein has a few barebones mills that are suited to the DIY-inclined brewer. You can get a basic mill and mount it in any mill housing design of your choice. They offer a 2-roller mill, 3-roller mill, and a 2-roller mill that can also crush corn. All of these have knurled hardened steel rollers and bronze bushings.
Mills to avoid[edit]
- The Barley Crusher - It has soft rollers and soft/cheap bronze bushings, which lead to relatively frequent problems and a short product lifespan.[18] Their customer service is also very poor.[19]
- Suspicious budget mills such as the motorized and 3-roller mills at Vevor - These cheap mills have a number of bad reviews and generally don't have a strong track record, so we don't recommend these products at this time.[20]
- Non-roller mills such as food processors, rolling pins, or Corona/Victoria style disc mills (example)[21] - These tools are not designed to create a proper crush, they're not easily adjustable, they tend to create a mess and/or require significant modification just to be useable.[22] Corona-style mills are generally low-quality products (e.g. they may add metal shavings to the grist). Buy pre-milled grain until you're ready to invest in a roller mill.
Mounting the mill[edit]
It is important to set up the mill on a base to keep the frames aligned properly. If the frames aren't straight, the rollers may bind.[23] As you are securing it to the base, make sure all the rollers spin freely. Most mills either come with a base or have one available. These bases are typically designed to let the mill sit on top of a plastic bucket, and this setup is fine in most cases. However if you are adding a dedicated motor, it will be necessary to attach the mill to a larger base or table.
Monster Mill accessories like this base will also work for the Kegco 3-roller mill.
Driving the mill[edit]
Three options exist for powering the mill. Any of these options can produce a good crush, so the choice of power just depends on your personal preference and budget. Warning: We do not recommend driving the mill with a hamster.
- Hand crank
- Electric drill
- Electric non-drill motor
Hand crank[edit]
A hand crank is available for many models, and attaches to the drive shaft with a screw. It is operated by turning the crank handle. This may get tiring for milling large amounts of grain.
Electric drill[edit]

For most home brewers a drill is the preferred method to drive a mill. It is easier to set up and more economical than using a non-drill motor, and significantly less laborious than hand cranking. Low RPM drills provide the best torque. We don't recommend using an external speed limiter (example) on a high RPM drill because they significantly reduce the torque.[24][25] Affixing a zip tie, 2" tri-clamp, or U-bolt to the trigger of a variable speed drill can help control and maintain a constant speed. A corded drill is generally more powerful than a cordless one, and will usually last longer. However cordless drills can also work well.[26][27] The one requirement to using a drill is that the drill chuck fits onto the mill drive shaft (which range from 3/8" to 1/2" [9-12mm]). If you are holding the drill while milling, you must also hold down the base of the mill. Otherwise the torque may cause the mill to flip over, causing damage to equipment and/or personal injury.
Bauer corded drill from Harbor Freight | 1/2" chuck, 0-600 rpm, variable speed. These are tried and true, and are frequently recommended by home brewers due to the low cost. |
Greenworks 24V cordless drill (Amazon) | 1/2" chuck, 0-380 rpm (also has higher speed setting), variable speed, brushless. |
Non-drill motor[edit]
Some brewers prefer using a dedicated non-drill motor. See Motorizing a mill.
Reducing torque requirement[edit]
If your drill/motor is having issues with stalling, or you'd like to reduce the load on it in order to extend its life, or you are wanting an easier job of hand cranking, you can reduce the amount of torque needed to drive the mill by reducing the amount of grain feeding into the rollers. All you need to do is create and affix cardboard inserts into the bottom of the hopper.
Setting the gap[edit]

All of the mills we recommend have an adjustable roller gap. A tighter gap produces smaller grain particles, called a fine crush, and a larger gap creates a coarse crush. There is not a one-size-fits-all gap setting. The ideal mill gap setting is dependent on your mill, your brewing system, and factors related to the grain (which can vary even from batch to batch and with storage time).[2][28][29] For each batch, the objective is to find an acceptable middle ground between lautering/recirculation effectiveness, efficiency (yield), and quality.[30][31] Some experimentation with different settings is needed to find out what works best for your mill and your brewing system, although there is a wide range that will be adequate.[32] Also, the grist should be visually monitored every milling to ensure it is being properly crushed.
There are two main things to consider when experimenting with the roller gap:
- The gap must be small enough so that all the kernels are crushed, which helps to maximize efficiency. This can easily be verified by milling about a cup of grain and visually inspecting it (carefully sort through it looking for uncrushed kernels).[33]
- The gap must be large enough to avoid problems with a stuck mash or slow lautering/recirculation.[22][33][34][35] This greatly depends on your system/process, and experimentation is required to find the smallest acceptable gap. For example, a simple BIAB system can tolerate a fine crush, whereas a recirculating system tends to benefit from more intact husks. Keep in mind that excessive husk damage can potentially affect beer quality (see below).[3] Also be aware that 2-roller mills have a lower limit at which the rollers can feed the grain.
For most systems, a gap in the range of 0.025" to 0.050" (0.7–1.2mm) is appropriate.[11][36] To measure this, a feeler gauge (which is a stack of metal pieces with different marked thicknesses) can be inserted into a gap to precisely measure it. To achieve gaps that are not the same as a single blade, stack multiple blades together to add up to the gap you want to set. In a pinch, a standard credit card can be used to set a 0.030" (0.76mm) gap.[37] If you have a 3-roller mill, an angled feeler gauge should be used because a straight feeler gauge cannot access the adjustable gap while the mill is assembled.
Straight feeler gauge (Amazon) | Blades range from 0.001" to 0.040" (0.03mm to 1mm) |
Angled feeler gauge (Amazon) | Blades range from 0.005" to 0.020" (0.127mm to 0.508 mm) |

Process:
- Insert the gauge into a loose gap and then gently tighten the rollers on it. The blades should go into the gap between the rollers with a minimum amount of force, and should not be crushed in the gap. Adjust the gap on both ends of the roller to be the same.[4][38]
- On mills with adjustment knobs, mark on the frame what the gap is at the a variety of knob positions. This allows you to repeat different gap settings without needing the feeler gauge again. We suggest marking increments every 0.005" (0.1mm) over a range of 0.020" to 0.055" (0.5–1.4mm).
Milling considerations[edit]
Several things should be considered when deciding on mill gap and other parameters that will affect grist performance during mashing.
Husk integrity[edit]
Pulverizing the entire grain into flour should generally be avoided.[39][40][35] A high percentage of flour will increase the viscosity of the wort, increasing the likelihood of the dreaded "stuck mash" or slow recirculating and lautering. We want the husks to be as intact as possible, not only for filtering, but also because finely shredded husks can cause astringent, bitter, or harsh off flavors.[1][39][41][42][43][44][45] Excessive milling promotes the extraction and solubilization of undesirable compounds into the wort and beer, such as silicates, lipids, husk-derived tannins (phenolic compounds), and large-molecular proteins, which can cause excess formation of trub, deposits, color changes, hazes, and a shorter shelf life.[2][46][47][39][48][49][50] Lastly, too much husk flour can potentially result in loss of extract because starch will be adsorbed to the husk and discarded with it.[51]
However, fine milling does not necessarily cause extraction of harsh flavors, and it can be acceptable depending on the lautering method.[22][52] Mash pH strongly influences the extraction of negative compounds, which can be particularly troublesome when fly sparging. Therefore the issue of undesirable flavor extraction from pulverized husks may be less worrisome for home brewers who properly control mash and sparge pH, although husk pulverization may still lead to other issues such as haze and excessive trub depending on other factors.[53]
Husk integrity can be improved by conditioning the grain, using an appropriately large mill gap, and using a 3-roller mill or a mill with fluted rollers.
Milling speed[edit]
In general, a milling speed between 50–300 RPM is considered appropriate for small scale milling.[54][11][4] Be aware that it usually takes a little more torque to get the mill going. If your drive method is struggling, use the method to reduce torque described above.
Some home brewers have found that milling at a lower speed reduces damage to husks.[55][54][56][57] Other brewers have not noticed a significant effect of milling speed on the grist (appearance or granulometry),[58][59] which is in agreement with professional literature.[40][3]
Oxidation[edit]

The grist begins to oxidize immediately upon milling (because the inside of the kernels are then exposed to air and moisture) and this can have a negative impact on the subsequent beer quality.[2][44][60][61] Therefore the time between milling and dough-in should be kept as short as possible.[49]
Modern commercial low oxygen breweries fill all areas containing milled grain with inert gas (CO2 or N2) to prevent oxygen exposure.[2][22][44][52][49] Brewers looking to preserve fresh grain flavor may do this simply by flowing inert gas into the bottom of the mash tun and milling directly into it, or by flushing the grist with inert gas after milling.[62][63][64][65] Purging a mostly covered mash tun at 1–2 psi for about 10 minutes has been shown to effectively remove the vast majority of oxygen in the vessel.[66] A regulator may start to freeze up and/or significantly chill the mash tun parts, causing dough-in temperature to be too low. A fix for that is to get a cheap heat lamp or hair dryer and point it at your regulator.[65] Dry ice can also be used to purge: put the dry ice in a jar with water and connect it with tubing to the mash tun. Note that flushing with inert gas during the actual milling process appears not to be critical, as oxidation does not occur immediately (at least with regard to lipids or proteins).[67][63]
Grain moisture[edit]
The moisture content of the malt influences the fineness of the grist. Moisture makes the grain more elastic and the crush becomes more coarse. Coarse particles adhering to the husks are more difficult to degrade during the mashing process, leading to a lower yield. This mainly applies to malts which, if improperly stored, have a water content of 8–12%. Unlike with grain conditioning, this moisture is distributed through the entire grain. On the other hand, a malt with very little moisture has a tendency to be crushed too fine, destroying the husks and increasing the flour content. This may occur when very young dark malts are used, which is probably an unlikely situation for home brewers. Conditioning may help avoid problems in both of these cases, although minimizing moisture during grain storage is still a high priority.[44]
Specialty grains[edit]
Lighter color kilned or dry roasted specialty malts will crush like base malts, while caramel/crystal and extremely dark roasted products are more brittle and tend to shatter rather than crush. Malts that shatter tend to create more flour which can contribute to difficulties during lautering. The fine particles can fill in the spaces in the otherwise permeable bed causing a slowed or stuck lauter. These brittle specialty malts can typically be milled with a wider mill gap resulting in a larger particle size that will still allow for complete flavor and aroma extraction which is the primary function of these malts. Finding the balance of desired particle size starts with adjusting the mill gaps.[68]
Wheat, rye, and oats
Generally speaking, these grains have smaller kernels (especially rye)[69] and are harder than barely. Therefore the mill gap may need to be decreased when milling these grains, and more torque may be required while milling. Mill small samples to check for whole kernels, just as we suggested above for setting the gap for barley. Take note of the ideal gap for each grain.
Things that don't need to be milled
- "Flaked" or "rolled" grain adjuncts do not need to be milled, although they can be run through the mill with the rest of the grain if it is convenient.[70]
- Rice hulls should not be put through the mill because their whole purpose is to remain intact in order to aid filtering.
- Most home brew mills are not suitable for milling corn.
- Fingers, clothing, rocks, or bits of metal should not be milled. Please be careful, especially when using power tools.
Dust[edit]
To avoid excessive dust contaminating your gear and wort, it's considered prudent to mill away from your cold-side gear and away from where you'll be chilling and fermenting your wort, particularly if you do not condition the grain. Conditioning can help lower the amount of dust generated while milling. However, dust can still be created when measuring the grain. Wearing a mask can be beneficial for your health since breathing in grain dust is not so great.[1] Thanks to COVID-19 you do have a mask, right?
Conditioning the grain[edit]

Dry husks fragment easily, which may cause issues (see above). Husks become more elastic when they are moist, making them easier to protect.[2][71][11][55][72][28][22][16] Increasing the moisture content of the grain husk right before milling is called "conditioning". The goal is to increase it just enough to minimize shredding as the grain passes through the mill. Generally the amount of water added should be about 1–2% of the weight of grain.[44][2][39][51] It's important not to add too much water because our mills cannot process wet grain; it will stick to the rollers. The recommended amount of moisture is low enough that the grain should not be sticky and it will not cause rollers to rust. Wheat malt also benefits from conditioning even though it is huskless.[73]
Conditioning is not a necessary step, but it does have advantages when combined with a proper roller gap.[39] The roller gap may need to be (and probably should be) tightened when conditioning, to make sure all the grains get crushed and to reap the benefits of more finely crushed starch.[74][28][22] Basically all modern commercial German breweries that use lauter tuns (as opposed to mash filters) either condition their malt or mill it wet.[73]
Advantages:
- Dust is reduced during milling.[55][15]
- The risk of dough balls is decreased.[55]
- The rollers may grip the grain better and feed faster.[55]
- Improved husk integrity provides a looser grain bed and easier lautering.[2][39][22][15]
- More intact husks means that the grain can be ground more thoroughly (tighter gap) without affecting lautering.[2][39][22][44]
- A tighter gap means that the starch is crushed more thoroughly.
- More thoroughly crushed starch means that efficiency and attenuation are increased and conversion is faster.[2][44][22]
- Reduced husk damage can have quality benefits on the resulting beer. (See above)
- Manually stirring and looking at your grain allows you to find any rocks, metal pieces, or other foreign objects that may be mixed with the grain and could otherwise damage your mill.
Disadvantages:
- Additional time and labor is required.
- Milling may require additional torque.
- A roller gap adjustment is probably needed to optimize crush (and prevent uncrushed kernels).[22]
- Protein extraction may be higher.[39]
Conditioning Method 1 (Editor's Choice)[55]
- Put the grain into a wide plastic tub.
- Add water to a small spray bottle.
- Spray the grain evenly while stirring (e.g. with your hand or a mash paddle) until the grain becomes pliable.
- The grain may be milled about 10 minutes after wetting.
View this method in action:
Conditioning Method 2 (no stirring)[11]
- Weigh out the grain in buckets.
- Add water to a small spray bottle.
- Pour a thin layer into a wide plastic tub.
- Spray it with water from a spray bottle.
- Repeat steps 3 & 4 until done.
- The grain may be milled about 10 minutes after wetting.
Conditioning Method 3 (sink sprayer)[11]
- Put the grain into a wide plastic tub.
- Attach a flexible misting nozzle to a sink hose.
- Spray the grain evenly while stirring (e.g. with your hand or a mash paddle) until the grain becomes pliable.
- The grain may be milled about 10 minutes after wetting.
If you are using a disc mill (like a Corona/Victoria style mill) instead of a roller mill, different amounts of moisture can possibly have variable and unpredictable effects on the resulting crush.[48] Therefore we cannot recommend conditioning when using such a mill, but you may still experiment if you wish.
For images comparing conditioned vs unconditioned grist, see here: Grain Conditioning at LOB. and Malt Conditioning at German Brewing.
Cleaning and maintenance[edit]

First time cleaning: After adjusting the gap, mill about a pound of grain and then throw that away. This removes the machine oils from the rollers.
Cleaning after use: A paintbrush and compressed air will remove dust and any grain and dust clinging to the rollers. A stainless steel brush can help remove stubborn particles.
Removing and preventing rust: Most mills have hardened steel rollers, so it is possible for them to rust. Running about a pound of grain or rice through the mill may be all that's needed to remove rust from the rollers. If that doesn't work, brush the affected area with a stainless steel brush until the rust is gone. Dust attracts moisture, so keeping the mill clean as described above will help prevent the rollers from rusting,[22] as will storing the mill in a dry location. If you condition your grain, consider reserving a half pound of unconditioned grain to mill at the end to remove any moisture.
Maintenance: The mills we recommend are fairly maintenance-free, particularly if you have one with sealed ball bearings and if you clean the rollers after use. However, mills (especially those with bronze bushings in particular) may benefit from periodic cleaning: disassemble, wipe clean, and lubricate. Visually check the gap setting before milling to make sure the adjustable gap is not slipping and that the rollers are in proper alignment. Rollers out of alignment may bind. Rollers with stubborn grain stuck between the knurling can be cleaned with a short (e.g. 30 minute) hot alkaline bath (see cleaning), although some rust will likely need to be removed afterwards.
Stainless steel brush | Amazon |
Food-grade machine oil for lubrication | Amazon |
Sieve testing[edit]
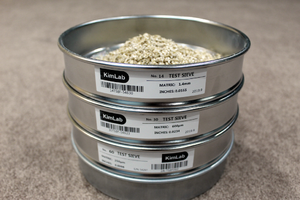
Sieves can be used to scientifically measure the particle sizes of the grist. This is called granulometry, or sieve testing. Unfortunately, the sieves are a bit expensive and the testing process is somewhat labor-intensive. Furthermore, the results are borderline useless since the crush produced by home brew mills differs greatly from that of a commercial mill, even with similar granulometry results.[59] Therefore, we do not recommend home brewers invest in the materials or effort required for sieve testing.
Our recommendation notwithstanding, sieve testing can be used in combination with visual inspection to compare how different milling parameters can affect the crush, and it can be helpful to maintain a tight degree of consistency through periodic testing. Large breweries use a machine to conduct the test, but it can also be done by hand using a standardized protocol, which has been shown to produce satisfactory results.[75][76] See Sieve testing for more information.
See also[edit]
External links:
- Video from Integrity Homebrewing comparing the effects of different mill gaps, mill speeds, and grain conditioning (20 minute video)
- Mills and Milling by Dave Miller, author of Brew Like A Pro
- If you're really into DIY: Suggestions to help build a mill from scratch
References[edit]
- ↑ a b c Mosher M, Trantham K. Brewing Science: A Multidisciplinary Approach. 2nd ed. Springer; 2021.
- ↑ a b c d e f g h i j k l m n Kunze W. Wort production. In: Hendel O, ed. Technology Brewing & Malting. 6th ed. VLB Berlin; 2019:203–218.
- ↑ a b c d e Mousia Z, Balkin RC, Pandiella SS, Webb C. The effect of milling parameters on starch hydrolysis of milled malt in the brewing process. Process Biochem. 2004;39(12):2213–2219.
- ↑ a b c FAQs. Monster Brewing Hardware. Accessed May 2020.
- ↑ Grain mill recomendations. Homebrew Talk website. 2019. Accessed 2020.
- ↑ Quality corona/hand-crank mill? Homebrew Talk website. 2018. Accessed 2020.
- ↑ Tell me about grain mills. Homebrew Talk website. 2019. Accessed 2020.
- ↑ Grain mill recomendation. Homebrew Talk website. 2019. Accessed 2020.
- ↑ Layosa C. Introduction to working with linear bushings: bushings vs. bearings. Misumi website. 2016. Accessed 2020.
- ↑ Ball Bearings vs Bushings. ServoCity on YouTube. 2017. Accessed 2020.
- ↑ a b c d e f Choosing a malt mill. The Modern Brewhouse website. 2018–2020. Accessed 2020.
- ↑ Monster mill problems. Homebrew Talk website. 2009. Accessed 2020.
- ↑ Carbon steel vs stainless steel. Reliance Foundry. Accessed June 2020.
- ↑ 3 roller homebrew grain mill. Monster Brewing Hardware. Accessed June 2020.
- ↑ a b c Evans E. Mashing. American Society of Brewing Chemists and Master Brewers Association of the Americas; 2021.
- ↑ a b Miedl-Appelbee M. Brewhouse technology. In: Stewart GG, Russell I, Anstruther A, eds. Handbook of Brewing. 3rd ed. CRC Press; 2017.
- ↑ "MattMill Kompakt / Kompakt Komfort documentation." MattMill. 2018. Accessed 2020.
- ↑ Grain mill stopped working. Homebrew Talk website. 2018. Accessed 2020.
- ↑ Barley Crusher - customer service???? Homebrew Talk website. 2012–2018. Accessed 2020. (This webpage has since been deleted. That's one more reason not to trust homebrewtalk.com)
- ↑ Anyone try those cheap eBay motorized grain mills? Homebrew Talk website. 2020–2021. Accessed Jan 4 2021.
- ↑ My ugly junk- Corona mill station. Homebrew Talk website. 2008–2020. Accessed 2020.
- ↑ a b c d e f g h i j k Briggs DE, Boulton CA, Brookes PA, Stevens R. Brewing Science and Practice. Woodhead Publishing Limited and CRC Press LLC; 2004.
- ↑ "Monster Mill MM 2/3/PRO Instructions." Monster Brewing Hardware, 2015.
- ↑ Speed controller for corded drill, used for milling grain? Homebrew Talk website. 2017. Accessed 2020.
- ↑ Monster mill drill question. American Homebrewers Association website. 2015. Accessed 2020.
- ↑ Need drill recommendations. BeerAdvocate website. 2018. Accessed 2020.
- ↑ Proper drill for milling grain. American Homebrewers Association website. 2011. Accessed 2020.
- ↑ a b c Crescenzi AM. Factors governing the milling of malt. J Inst Brew. 1987;93:193–201.
- ↑ Delucchi V. The perfect crush. Brew Your Own website. 2019. Accessed January 2021.
- ↑ Hansen B. Practical milling for the craft brewer. Briess Malt & Ingredients Co. 2007. Accessed 2020.
- ↑ Holbrook CJ. Brewhouse operations. In: Smart C, ed. The Craft Brewing Handbook. Woodhead Publishing; 2019.
- ↑ Mashing for high gelatinisation temps. The Modern Brewhouse website. 2020. Accessed 2020.
- ↑ a b Miller D. Mills and milling. Brew Like A Pro website. 2012. Accessed 2020.
- ↑ Kühbeck F, Dickel T, Krottenthaler M, et al. Effects of mashing parameters on mash β-glucan, FAN and soluble extract levels. J Inst Brew. 2005;111(3):316–327.
- ↑ a b Kallmeyer M. To mash or not to mash Kurz/Hoch. Drayman's Brewery website. 2016. Accessed online March 2024.
- ↑ Dry crush mill gap. The Modern Brewhouse website. 2018. Accessed 2020.
- ↑ "ISO/IEC 7810." Wikipedia. Accessed May 2020.
- ↑ Ream J. How to: adjust the mill gap of a barley crusher. Homebrew Engineer blog. 2015. Accessed 2020.
- ↑ a b c d e f g h Szwajgier D. Dry and wet milling of malt. A preliminary study comparing fermentable sugar, total protein, total phenolics and the ferulic acid content in non-hopped worts. J Inst Brew. 2011;117(4):569–577.
- ↑ a b Warpala IWS, Pandiella SS. Grist fractionation and starch modification during the milling of malt. Food and Bioproducts Processing. 2000;78(2):85–89.
- ↑ Homebrew grain mills and a pictorial guide to milling grain. Winning-Homebrew.com website. Accessed May 2020.
- ↑ Whitting C. "Milling Your Grain." Beer & Brewer. 2018. Accessed 2020.
- ↑ Brown R. Homemade grain milling systems. MoreBeer. Accessed May 2020.
- ↑ a b c d e f g Narziss L, Back W, Gastl M, Zarnkow M. Abriss der Bierbrauerei. 8th ed. Weinheim, Germany: Wiley-VCH Verlag GmbH & Co. KGaA; 2017:126–130.
- ↑ Fix G. Principles of Brewing Science. 2nd ed. Brewers Publications; 1999.
- ↑ Zepf M. Milling. Craft Beer & Brewing. Accessed May 2020.
- ↑ Siebert KJ. Haze formation in beverages. Lebenson Wiss Technol. 2006;39(9);987–994.
- ↑ a b Pereira de Moura F, Rocha dos Santos Mathias T. A comparative study of dry and wet milling of barley malt and its influence on granulometry and wort composition. Beverages. 2018;4(51).
- ↑ a b c Golston AM. The impact of barley lipids on the brewing process and final beer quality: A mini-review. Tech Q Master Brew Assoc Am. 2021;58(1):43–51.
- ↑ Prechtl C. Some practical observations concerning grain bitterness in beers and its amelioration. Tech Q Master Brew Assoc Am. 1967;4(1):98–103.
- ↑ a b Krottenthaler M, Back W, Zarnkow M. Wort production. In: Esslinger HM, ed. Handbook of Brewing: Processes, Technology, Markets. Weinheim, Germany: Wiley-VCH Verlag GmbH & Co. KGaA; 2009.
- ↑ a b De Rouck G, Jaskula-Goiris B, De Causmaecker B, et al. The impact of wort production on the flavour quality and stability of pale lager beer. BrewingScience. 2013;66(1/2):1–11.
- ↑ De Rouck G, Jaskula B, De Causmaecker B, et al. The influence of very thick and fast mashing conditions on wort composition. J Am Soc Brew Chem. 2013;71(1):1–14.
- ↑ a b Conditioned grain mill gap. The Modern Brewhouse website. 2017–2018. Accessed 2020.
- ↑ a b c d e f Revisiting grain conditioning. The Modern Brewhouse website. 2018–2019. Accessed 2020.
- ↑ So what's the right Harbor Freight drill for a mill? 20% off coupon out now. Homebrew Talk website. 2020. Accessed 2020.
- ↑ Best place to get a grain mill. Homebrew Talk website. 2022. Accessed May 27, 2022.
- ↑ Milling test results. The Modern Brewhouse website. 2020. Accessed July 2020.
- ↑ a b Bittner A. Think like a scientist: Sieve testing. Brewing Forward website. 2021. Accessed February 2021.
- ↑ Pascoe HM, Ames JM, Chandra S. Critical stages of the brewing process for changes in antioxidant activity and levels of phenolic compounds in ale. J Am Soc Brew Chem. 2003;61(4):203–209.
- ↑ Cheynier V. Polyphenols in foods are more complex than often thought. Am J Clin Nutr. 2005;81(1):223S–229S.
- ↑ Stephenson WH, Biawa JP, Miracle RE, Bamforth CW. Laboratory-scale studies of the impact of oxygen on mashing. J Inst Brew. 2003;109(3):273–283.
- ↑ a b Muller R. Use of 5,5’-dithiobis (2-nitrobenzoic acid) as a measure of oxidation during mashing. J Am Soc Brew Chem. 1995;53(2):53–58.
- ↑ CO2 purge of mash tun prior to underletting? The Modern Brewhouse website. 2018. Accessed 2020.
- ↑ a b Milling into mash tun. The Modern Brewhouse website. 2019. Accessed 2020.
- ↑ Purging grist in the tun. The Modern Brewhouse website. 2018. Accessed 2020.
- ↑ Wackerbauer K, Meyna S, Marre S. Hydroxy fatty acids as indicators for ageing and the influence of oxygen in the brewhouse on the flavour stability of beer. Monatsschrift Brauwiss. 2003;56(9/10):174–178.
- ↑ Geurts J. 9-5 grind. Briess blog. 2018. Accessed 2020.
- ↑ Howe S. Raw materials. In: Smart C, ed. The Craft Brewing Handbook. Woodhead Publishing; 2019.
- ↑ Brewers barley flakes. Briess Product Information Sheet. 2019. Accessed 2020.
- ↑ Rabe B. Grain Conditioning. The Modern Brewhouse website. 2016. Accessed 2020.
- ↑ Venturini Filho WG, Nojimoto T. Utilization of the wet milling malt steep water as raw material on brewing. Ciênc Tecnol Aliment. 1999;19(2):174-178.
- ↑ a b Troester K. Malt Conditioning. German brewing and more wiki. Updated 2009. Accessed 2020.
- ↑ Seriously bad mash efficiency suddenly! The Modern Brewhouse website. 2019. Accessed 2020.
- ↑ Malt grist by manual sieve test. J Am Soc Brew Chem. 2003;61(4):246–249.
- ↑ Schwarz P, Barr J, Joyce M, Power J, Horsley R. Analysis of malt grist by manual sieve test. J Am Soc Brew Chem. 2002;60(1):10–13.